In the area of additive manufacturing we concentrate on the extrusion based technology of thermoplastic materials. For the development of filaments, with defined properties, we can rely on the know how from compounding, the material measurements and also extrusion. besides of the material the great number of printing parameters and the design are from great importance for the quality of the parts.
We are part of AM@MUL
At Montanuniversität, a group of more than 60 researchers are working in the field of additive manufacturing and have now joined forces in the AM@MUL network. → More information can be found here
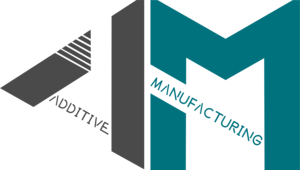
3DMultiMat - 3D Printed Functional Multi-Material Components
The goal of this three-year (2020-2022) project is to develop a sustainable, stable and flexible manufacturing process for complex multi-material (metal-ceramic) components shaped via extrusion-based additive manufacturing followed by sintering. Two material combinations are investigated. In the first material combination electrically conductive and insulating sections of ceramics are combined. The second area is the manufacture of metal components with sections of magnetic and non-magnetic properties as well as electric conductive and non-conductive properties.
The Institute of Polymer Processing at the Montanuniversitaet Leoben is leading the project, which has received funding from the Austrian-Chinese Cooperative RTD Program by the Austrian Ministry for Transport, Innovation and Technology (bmvit) and the Austrian Research Promotion Agency (FFG). The Austrian industrial partner is RHP Technology and the Chinese partner is the Institute of Metal Research at the Chinese Academy of Science in Shenyang.
Förderung: Production of the Future, 29. Call, Bilateral Cooperation Austria – Chinese Academy of Sciences, CAS, China »Project website of FFG
Laufzeit: 01.01.2020-31.12.2022
Partner: RHP-Technology GmbH, Institute of Metal Research (IMR), Chinese Academy of Sciences (CAS)
addmanu
In the flag ship project Addmanu the chair researches the thermal and rheological properties of the filaments for 3D printing and correlations between these properties and the printed parts should be found. With the optimized process parameters the quality of the printed parts should be increased. With the project partner Hage alternative feeding devices should be developed.
Further information in the biennial report 2017 - 2018 (page 28)
Further information in the biennial report 2013 - 2014 (page 23)
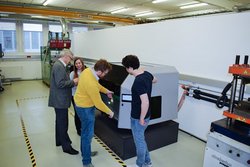
AM4I
The FFG CORNET project AM4I (Additive Manufacturing for Industry) focuses on quality-assured 3D printing processes for the production of technical components from high-performance polymers and hybrid constructions in the SME environment.
The core idea of ??the project is to fit additional manufacturing technologies (Fused Filament Fabrication (FFF)) for industry in terms of quality, time and costs. Metal-, ceramic- and polymer-printing are taken into account and the entire value-added process of material - print - component is illuminated.
The Chair for Polymer Processing deals with three specific case studies from the automotive, filament extrusion and orthopedics.
Further information in the biennial report 2015 - 2016 (page 50)
CerAMfacturing
In this project the additive manufacturing of ceramic should be developed for consumer goods and medical devices, which are impossible to produce with other techniques. The chair develops ceramic polymer compounds, but also electrically conductive materials for fused filament fabrication. These should be printed at the same time and after sintering form a compact part with customised and multifunctional components.
This project has received funding from the European Union’s Horizon 2020 Research and Innovation Programme.
Partner: Fraunhofer-Institut für keramische Technologien und Systeme, Admatec, Ceramicx Ireland Ltd, et al.
Further information in the biennial report 2015 - 2016 (page 42)
The efficiency and reliability of power electronics depends very much on the temperature. Growing demands to reduce the size of electronic components leads to the use of new technologies and materials, while ensuring efficient cooling and economical production.
The ECOPRINT project addresses these needs by developing new metal-polymer and metal-organic hybrid compounds for use in additive manufacturing. The development steps are the functionalization of metallic and ceramic powder particles by atmospheric plasma or wet chemical processes, incorporation of these powders into high performance polymers, optimization of filaments, modification of equipment for processing by additive manufacturing and investigation of new materials for high temperature applications.
Further information is available at www.ecoprint.co.at
Funding: Austrian Research Promotion Agency (FFG), M-ERA.NET
Duration: 01.08.2018-31.07.2021
Partner:Siemens, plasmatreat, IFAM Bremen, TU Bergakademie Freiberg, Cubicure, EVO-tech
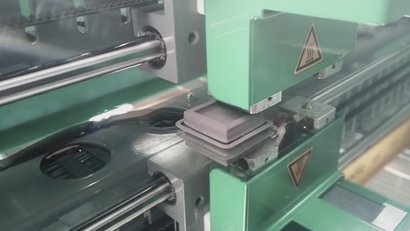
FlexiFactory3Dp
Flexible production via 3D printing of sintered metal and ceramic complex parts
The goal of this two-year (2017-2019) project is to develop a sustainable, stable and flexible manufacturing process for complex metallic and ceramic components shaped via extrusion-based additive manufacturing. Among the applications of this process in the project are the manufacturing of monolithic catalysers for air purification and components for the mobility industry.
The Chair for Polymer Processing is leading the project, which has received funding from the Austrian-Chinese Cooperative RTD Program. The Austrian industrial partner is RHP Technology, and the Chinese partners are the Research Center of Nano Science and Technology at Shanghai University and the Shanghai Industrial Technology Institute.
Further information in the biennial report 2017 - 2018 (page 27)
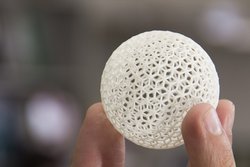
Natural3D
The core idea of ??this two-year project is to print biofiber-reinforced polymers on free-form surfaces along the flow to maximize the components.
The Chair for Polymer Processing, together with the Kompetenzzentrum Holz Wood K Plus (consortium leadership), has received funding for the project "Natural3D" from the call "Austrian-Chinese Cooperative RTD Projects".
The other project partners are FH Technikum Wien, Hage GmbH CoKG, Ecoplus, Thermoplastkreislauf GmbH, HeadSport GmbH, Haratech GmbH and Shiner3D GmbH.
NextGen 3D
The FFG cooperation and innovation project NextGen3D deals with the materials development for the industrial additive manufacturing. Polyolefins should be developed and optimized for extrusion-based additive manufacturing, as such polymers are not commercially available. The impact strength and the heat deflection temperature of the polyolefins are higher than the normally used polymers for extrusion-based additive manufacturing.
In addition, polypropylene is to be tested for filament production, which is characterized by a higher toughness, good modifiability, lower moisture absorption and better temperature and chemical resistance compared to commercially available filaments of ABS or PLA.
Further information in the biennial report 2013 - 2014 (page 29)
Further information in the biennial report 2017 - 2018 (page 26)
REProMag
The goal of this EU funded project is the development of a resource efficient manufacturing route for Rare-Earth magnets. At the chair a polymer metal compound is developed, which should be used on fused filament fabrication printers (FDM printer). The printed parts are put into a solvent to remove the first polymeric compounds and afterwards the parts are sintered to get homogenous rare earth magnets.
Project funded by the European Union’s Horizon 2020 research and innovation programme.
Further information in the biennial report 2015 - 2016 (page 47)
Tribopolymers are becoming increasingly important in industry, especially in the field of drive engineering, and often generate new market demands. The used manufacturing technology plays a central role in the manufacture of products from these materials, both in terms of technical performance and economic features.
The Tripolfact project compares additive and conventional manufacturing as well as hybrid manufacturing technologies.
Download Info-Folder (in German)
Funding: The Tripolfact project is funded by FFG/BMWFW in the "COIN, Cooperation and Networks" programme.
Duration: 2018 - 2020
Partner:Heinz Ehgartner Gesellschaft m.b.H., EVO-tech GmbH, DI Karl Josef Schnetzinger, Polymer Competence Center Leoben GmbH, Faigle Kunststoffe GmbH
ARBURG freeformer 200-3X
- Additive Fertigung mit Standardgranulaten
- Austragseinheiten: 2
- Baufläche: 200 cm²
- Bauteilträger: 3-Achsen
Der freeformer wird dem Lehrstuhl für Kunststoffverarbeitung von der Firma ARBURG im Rahmen des Projektes CAMED zur Verfügung gestellt und wird die Verwendung der Additiven Fertigungstechnologien an der Montanuniversität Leoben weiter vorantreiben.
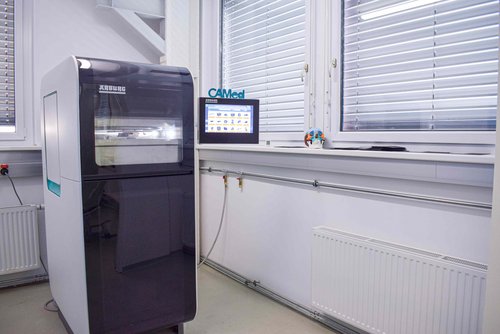