Chemistry of Polymeric Materials
With respect to research and teaching, the Institute of Chemistry of Polymeric Materials is active in the fields of
- Macromolecular chemistry
- Physical chemistry of polymeric materials
- Molecular characterization of polymers.
Research topics are
- Smart and Light-Reactive Polymers
- Functional Surfaces
- Sustainable Materials
The aspect of sustainability is covered in several of our projects. A number of cooperative research projects are conducted together with other universities, industrial companies and non-university R&D institutions.
News
Matchmaking in Leoben
07/03/2025
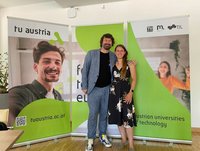
At the matchmaking event on energy transformation, Christine Bandl and Stefan Spirk presented the ‘Vanilla Flow’ project – an innovative approach to sustainable plastic applications of the future.
Half-yearly meeting of the EU project VanillaFlow in Leoben
05/19/2025
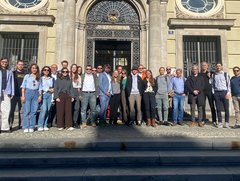
On 3 and 4 April 2025, the half-yearly meeting of the EU-funded research project VanillaFlow took place in Leoben. Partner institutions from several European countries came together to present the current progress of the project, discuss key results and define the next steps.
Innovative research on TV: hydrogen storage in polymers
11/11/2024
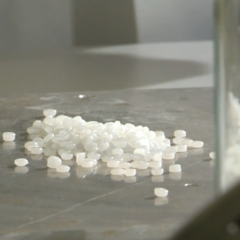
On November 6, 2020, an exciting contribution from the Institute of Chemistry of Polymeric Materials was broadcast as part of the program “Steiermark heute” (ORF 2, 7:00 p.m.).
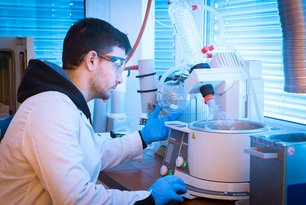
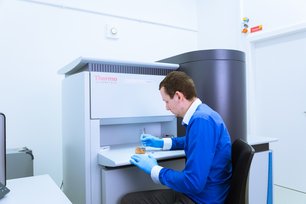
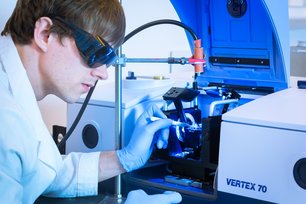
Research & Projects
Research Topics
With respect to research, the Institute of Chemistry of Polymeric Materials is active on both a fundamental and a technological level. Whilst fundamental research aims at the study of new polymeric materials and processes, technological research is in many cases being conducted together with industrial companies and non-university research organizations such as the Polymer Competence Center Leoben (PCCL) see www.pccl.at.
Multidisciplinary approaches, a strong interaction with polymer engineering, and a vivid collaboration with international research partners are the cornerstones of our research. The early involvement of students (bachelor and master level) in research projects is another element of our research policy, and significantly contributes to the academic education and professional experience of young engineers.
The Main Research Fields of the Institute of Chemistry of Polymeric Materials are:
Smart and Light-reactive Polymers
Additive Manufacturing allows for straightforward and customized production of complex 3D structures and components by a layerwise deposition of materials without the demand for special tools or molds. Along with subtractive manufacturing techniques such as milling or lathing and "formative manufacturing" such as casting or forging, "additive manufacturing" is considered as the third pillar of overall manufacturing technology.
In 1984, Chuck Hull developed stereolithography, the first additive process for polymers, which was commercialized a few years later. Subsequently, other techniques such as 3D inkjet printing, powder melting and fused deposition modelling were developed, which were initially used for the low-cost production of prototypes.
Through continuous improvement of machines and materials, these processes are increasingly being applied in industrial manufacturing processes for functional polymeric components. However, there are still limitations with regard to the production speeds and the building sizes of these methods as well as the surface quality, biocompatibility and the thermo-mechanical properties of the printed polymeric objects.
This explains the research efforts of the Institute of Chemistry of Polymeric Materials in the field of additive manufacturing. Numerous research projects (see below) focus on the investigation of novel photosensitive materials that pave the way towards new fields of application for additively manufactured polymeric components.
The production of medical devices by additive manufacturing technologies (AMT) has become a popular field of research in the last years as it allows for fabrication of complex and individually shaped geometries in short production times from 3D models that can be directly obtained from the patients’ X-ray, MRI or CT scans. AMTs based on the photo polymerisation of light sensitive resins, e.g. stereolithography (SLA), digital light processing (DLP) or 3D inkjet printing (3-DP), allow for fast and very precise production of complex structures with high surface quality and tuneable mechanical properties. State of-the-art resins are mainly based on acrylate and methacrylate building blocks which are well established in the decorative and protecting coating industry. They show fast curing rates, excellent storage behaviour as well as tuneable mechanical properties. One considerable drawback of this class of chemical compounds is their low biocompatibility.
Another drawback of radical cured photopolymers is their insufficient polymer toughness, which explains the brittleness of 3D manufactured parts. This behaviour can be attributed to the evolution of shrinkage stress during the fast radical chain growth polymerization and to an inhomogeneous polymeric architecture.
One focus of our research is set on the investigation of alternative radical based curing reactions to substitute (meth)acrylate monomers of conventional photosensitive resins, which provide biocompatibility, high toughness and flexibility in the cured state as well as biodegradability.
These advantages together with the possibility of tuneable degradability and surface modification make these photo-curable materials valuable candidates for the tailor-made fabrication of several types of medical devices (see Figures) via stereolithography.
Based on these developments, the spin-off Luxinergy GmbH (www.luxinergy.com) has been co-founded by Thomas Griesser focussing on the distribution and sale of resins and 3D printers for the manufacturing of orthopaedic orthoses and dental clear aligners.
Despite the continuous development of additive manufacturing techniques, these processes are still too slow for an efficient production of components and prototypes in series. For that reason, one has to rely largely on well-established production methods such as injection molding. One possibility to shift the profitability of additive techniques significantly to a higher number of parts provides rapid tooling in which injection molding tools for the production of polymeric parts are produced by means of additive manufacturing technologies.
Metallic tools, produced by laser melting or laser sintering, allow for similarly high numbers of produced items as tools fabricated by conventional methods, but are severely limited in terms of low surface quality and manufacturing efficiency. In contrast, additive processes based on photopolymerization provide good process efficiency, higher surface finishes, and do not require a post-treatment (e.g. grinding or polishing). However, tools made of photopolymers exhibit a very limited tool life, which can be explained by the low heat resistance and the brittleness of this kind of materials. To achieve the goal of a cost-effective and time-efficient production of robust injection-molding tools, novel photopolymers are being investigated. The developed resins exhibit high heat resistance and toughness in the cured state and can also be processed by means of stereolithography. The figure below shows an additively manufactured injection molding tool by means of stereolithography.
The development of stretchable, conductive materials paves the way towards an easy integration of multifunctional electronic sensor arrays in clothing, three-dimensional surfaces of machines, human skin or polymeric materials. One motivation for the development of such systems arises from the vision of realizing intelligent clothing and the integration of sensors on textile surfaces (smart textiles, e-textiles), respectively.
Besides the demand for a straightforward and cost-efficient fabrication process of elastomeric devices, also the stretchability of electric connections and contacts is a crucial functional prerequisite. For this purpose, new methods for the production of metallic nanoparticles without the need for toxic chemicals in an elastomeric matrix are developed.
Silver Based Conductive Composite Materials for Stretchable Electronics
For the realization of conductive composite materials self-reducing silver complexes have been evaluated. On the basis of these compounds, pastes and inks are being developed, which can be applied on sufficiently large substrates by screen or ink-jet printing. The printed conductors and electrodes show a very low resistance change with an elongation of up to 200%. In cooperation with Joanneum Research Weiz, AT & S and Human Research, a sensor patch (strain sensors, see Figure 1) for the monitoring and detection of heart and respiratory activity was developed.
Copper Based Conductive Composite Materials for Stretchable Electronics
The comparatively high price of silver represents a major disadvantage for the implementation of these technologies in industrial-scale production. This fact explains the research efforts of the recent years regarding the development of copper-based pastes for printed electronics. Copper offers the advantage of a much lower price (factor ~ 90) compared to silver with a similarly low specific resistance. The biggest challenge in the production of copper-based fillers is its high tendency for oxidation under the formation of non-conductive copper oxide. For this reason, the synthesis of such nanoparticle systems must be carried out under an inert gas atmosphere. In the course of our research, novel methods for the production of stretchable conductors based on self-reducing copper compounds are being explored. The developed pastes can be applied by screen printing and are subsequently converted into conductive structures (see Figure 2) by near-infrared irradiation without the demand of inert gas atmosphere.
Functional Surfaces and Coatings
The function of a material is often closely related to its surface properties rather than to those of the bulk. Therefore, the adjustment of surface properties plays a crucial role in many technical areas and industrial sectors. Important functions, which are determined by surface properties, reach from protection against corrosion, abrasion, condensation and fire, over self-cleaning, anti-adhesive, anti-fouling, anti-bacterial, anti-frost and anti-reflective properties to adhesion promotion and barrier effects. The surface properties of a material can be tailored either by the application of a coating or by surface modification. For this purpose, wet chemical methods such as silane chemistry, etching or polymer grafting as well as dry methods including flame treatment, corona discharge and plasma treatment can be employed. In order to examine the surface composition and properties, X-ray photo electron spectroscopy (XPS), attenuated total reflection Fourier-transform infrared spectroscopy (ATR-IR) and contact angle goniometry are available at our institute. In addition, atomic force microscopy (AFM) and SEM (EDX) are accessible at MU Leoben.
In addition to storing electrical energy in batteries, the conversion of green electricity into hydrogen can also help to switch energy generation completely to renewable sources. One method of producing hydrogen is water electrolysis. The basic process is very simple: water is cleaved into hydrogen and oxygen in an electrolyser using electricity. Thus, electrical energy is converted into chemical energy and stored. This process can ultimately be reversed to generate electrical energy (power supply). There are currently two systems in use for this water electrolysis: alkaline electrolysers and proton exchange membrane electrolysers. However, both techniques have disadvantages. One delivers a low current density and hydrogen quality, while the other requires a lot of material and is therefore expensive. In the AEM Neo project, a team of our Institute of Chemistry of Polymeric Materials is working together with employees of HyCentA Research GmbH to optimize a still very young approach: anion exchange membrane electrolysis cells (AEM-WE), which combine the advantages of conventional methods.
The project aims to take a decisive step towards higher performance and longevity. The focus is on optimizing the membrane electrode assembly (MEA) - the heart of water electrolysis. For conventional technologies, there are already mature membranes and ionomers or binders - these are the ion-conducting components with which hydrogen and oxygen can be separated in the cell. However, these binders in particular are not ideal for the use in AEM-WE. In this project new binder materials are developed and suitable manufacturing processes for the entire AEM-WE cell are investigated. The necessary infrastructure for the chemical modification and characterization of the binder materials is available in the laboratories of the Institute of Chemistry of Polymeric Materials while state-of-the-art testing facilities for testing the newly developed electrolysis cells are available at HyCentA.
The material of choice for the first tests is commercially available polytetrafluoroethylene (PTFE). PTFE is a universally applicable polymer, with low sensitivity to friction and high resistance against acids, bases, alcohols, etc. However, as PTFE is chemically inert, it is not intrinsically ion-conducting and is therefore not suitable as a binder in the AEM-WE membrane. To change this, PTFE is chemically modified at the Department of Chemistry so that protonizable groups are applied to the surface, which ensure the desired ion conductivity. In addition, the wettability is increased and the adhesion of gas bubbles is reduced. This is achieved by the use of various plasma-based methods and subsequent wet-chemical treatments. Finally, the modified binder is used to produce an AEM-WE cell and the influence of various parameters, such as the ratio between binder and catalyst, on cell performance is investigated.
More information is provided by Dr. Christine Bandl (christine.bandl(at)unileoben.ac.at)
In a recent project (Cornet-CARACOAT; cooperation with the University of Paderborn, Ecoplus Niederösterreich and several industrial partners) an anti-adhesive coating based on organosilane chemistry was developed. The coating reduced the demolding forces during injection molding of polymer parts by up to 90 % and prolonged the service life of the mold. Based on this performance and the covalent coupling to the substrate, the developed organosilane coating represents a promising alternative to conventional demolding aids such as silicon sprays, which have to be renewed after each demolding cycle.
Another highlight of the project was the development of a simple and rapid recoating method, in which the organic portion of damaged coatings is removed by flaming, and a secondary organosilane layer is attached by repeating the initial coating step (see Fig. 1).
More details about this procedure can be found in ScienceDirect. In a consecutive study, the organosilane coating is extended by a visibility-on-demand property. For this purpose, a fluorescent silane marker is incorporated into the silane layer, emitting blue fluorescence upon UV irradiation (see Fig. 2, MDPI). Further information is provided by Christine Bandl.
A coating with biocidal properties was designed to deactivate bacteria and viruses on photopolymer surfaces. This is a material class frequently used for UV-curable varnishes and coatings for furniture and flooring as well as for additively manufactured parts. The biocidal layer consists of copper nanoparticles, which are applied by immersion of the polymer part into an aqueous solution of the particles. The characteristic surface chemistry of the photopolymers allows for covalent coupling of the copper nanoparticles. Within 30 minutes the viral load of selected bacteriophages (i.a. test viruses for SARS-2 and influenza viruses) was significantly reduced or the viruses got even completely deactivated.
Besides coatings, also the direct modification of surfaces is addressed. The functionalization of inorganic surfaces by molecular layers, including self-assembled monolayers, is a widely applied and important technique for the fabrication of functionalized and nanostructured materials. By conferring photoreactivity to molecular layers at surfaces, various surface properties can be adjusted by UV illumination. This includes surface polarity, optical properties as well as chemical reactivity, thus enabling follow-up reactions utilizing the photogenerated groups. In combination with lithographic patterning, 2D structures are accessible on various substrates.
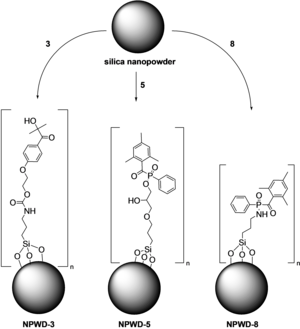
The coupling of free radical photoinitiators to nanoparticles was studied intensively. Photoactive fillers were designed by covalently attaching photoiniating groups onto silica nanoparticles. A series of tri(alkoxy)silyl functionalized acylphosphine oxides and other Norrish type I photoinitiators were synthesized and coupled to nanosilica. The modified particles were then incorporated into acrylate resins and thiol-ene resins to study the photoinitiation efficiency of the covalently bound initiators. The concept of using immobilized photoinitiators follows a general strategy towards low-migration photoinitiators as required for UV curable printing inks. Another approach is related to the immobilization of azidophenyl units onto the surface of inorganic particles. Using this approach, these particles (e.g., silica) can be attached to the surface of chemically inert polymer films and fibres such as polyethylene and poly(ethylene terephthalate) by a photoinduced click reaction. This paves the way towards inorganic protective layers on polymer surfaces, and also towards the tuning of properties of particle composites: the light induced attachment of nanoparticles to the matrix phase noticeably changes the mechanical properties of the composite, in particular, its brittleness. More information is provided by Wolfgang Kern and Sandra Schlögl.
For selected publications on this topic, see these links:
https://doi.org/10.1016/j.eurpolymj.2017.11.046
https://doi.org/10.1016/j.polymer.2017.09.054
https://doi.org/10.1002/pola.28442
https://doi.org/10.1016/j.compscitech.2019.107799
A current project deals with the immobilization of highly efficient photoinitiators based on acyl germanium compounds onto pre-activated inorganic surfaces. Different coupling mechanisms are being investigated. The grafting-from polymerization of various monomers including styrene as well as fluourescent acryates, hydrophobic monomers such as perfluoroalkyl acrylates and polar monomers (e.g., acrylamide) is performed. Using lithographic techniques, patterned surfaces combining hydrophilic and hydrophobic properties are realized. This research is being conducted in close cooperation with TU Graz (team of Michael Haas, Institute of Inorganic Chemistry) where the synthetic work on the germanium initiators is performed. Further information on this running project is provided by Matthias Müller and Christine Bandl.
A review on surface initiated photopolymerization has been published by us in Polymers 14, 608 (2022); see https://doi.org/10.3390/polym14030608
Sustainable Materials
Important activities of our institute are related to polymeric materials in the context of circular economy, renewable energies and sustainability. In the following some examples are shown where we contribute to the UN Sustainability Goals (UN SDG), also following the concepts of the European Green Deal. The projects range from thermal insulation over hydrogen storage to the up-cycling of polyolefin waste.
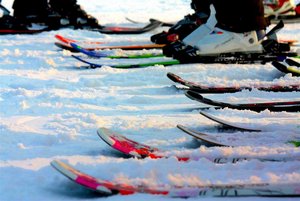
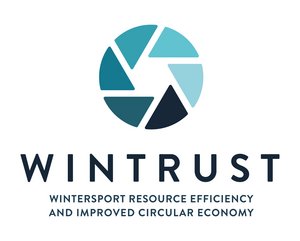
Winter sports equipment such as skis, bindings, ski boots, poles, and helmets unfortunately often end up as bulky waste at the end of their life cycle, thereby squandering valuable resources that could be used in the manufacturing of new products. The new interdisciplinary project WINTRUST aims to establish the groundwork for recycling winter sports equipment and achieving a closed-loop system.
Many materials utilized in skis, ski bindings, and boots are joint with robust adhesives to form a durable composite material. These adhesive bonds cannot be mechanically separated, such as through shredding, but require chemical dissolution. The Institute of Chemistry of Polymeric Materials is addressing this problem set within the WINTRUST project. Dissintegrating these adhesive bonds, particularly epoxy adhesives, presents a significant challenge. Traditional methods such as heating or treatment with acids often fail to achieve the desired outcome, as they may harm the remaining materials. Consequently, our scientists are exploring innovative approaches such as laser shock waves and microwaves to cause delamination of adhesive bonds.
Projectpartner: ecoplus. Niederösterreichs Wirtschaftsagentur GmbH (project management), Atomic, Head, Fischer, Blizzard – Tecnica, Leki, Komperdell, Isosport, Hexcel, Gabriel Chemie, Asma GmbH, SUNPOR Kunststoff GmbH, INTERSPORT Österreich, Bründl Sports, GW St. Pölten, Thermoplastkreislauf GmbH, SynCycle, Next Generation Elements GmbH, ZEMKA Gesellschaft m. b. H., Montanuniversität Leoben (Institute for Polymer Processing, Chemistry of Polymeric Materials and Processing of Composites and Design for Recycling), Transfercenter für Kunststofftechnik GmbH, Fachverband der Holzindustrie, VSSÖ – Verband der Sportartikelerzeuger und Sportartikelhänder, Österreichischer Carbon Cycle Circle ÖCC², RDG Recycling Group
More information is provided by Dr. Christine Bandl (E-Mail: christine.bandl@unileoben.ac.at)
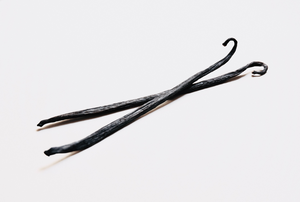
Redox flow batteries have been in use for a number of years to balance supply fluctuations from renewable energy sources and thus keep our power grid stable. They are long-lasting, inherently safe to operate and can be easily adapted to specific requirements - from small applications, e.g. in households, to large systems for load balancing. However, currently the main commercial technologies are based on unsustainable and toxic materials that also damage other battery components, making early replacement necessary. The consortium is coordinated by the start-up Ecolyte) &Graz University of Technology, and comprises the Spanish company Biobide, Darmstadt University of Technology and the Institute of Chemistry of Polymeric Materials at Montanuniversität Leoben is researching a holistic solution for sustainable flow batteries within the "VanillaFlow" project (funded by the European Union).
The aim of the project is to develop an environmentally friendly battery system which works with renewable raw materials that are readily available in the EU, and do not release any harmful substances during recycling. In particular, chemical structures of vanillin, the aroma component of the vanilla pod, and derived hydroquinones are being investigated. In a novel biotechnological process, vanillin will be converted with the help of modified yeasts so that it can be used as a redox-active molecule in a battery.
The application of milder reactive components also enables the use of more environmentally friendly materials for other battery components. For example, new paper-based membranes which serve as a barrier between the liquids in the battery will be developed, and the surface properties of the carbon felts - the electron conductors in the battery - are also optimized. In addition, artificial intelligence will be used here: Customized AI support systems will help in the development of the battery and in its integration into existing systems, as well as in the control of charging and discharging. Finally, the battery system developed will be integrated into the photovoltaic network on the TU Graz campus.
As part of the project, the Institute of Chemistry of Polymeric Materials at Montanuniversität Leoben is working on the modification of the surfaces of the carbon felts. As already described, these felts serve as electron conductors ensuring the flow of electrons to the current collectors. So far, this component of the battery has received little attention in research, which is now set to change. Due to surface functionalization, the conductivity of the felts will be improved - and the life time of the felts will be increased by reduction of fouling and deposits. For this purpose, selected methods for surface functionalization using wet-chemical and dry activation methods, as well as silanization and grafting approaches will be employed. This process is again supported by AI systems.
More information is provided by E-Mail: Christine Bandl (christine.bandl(at)unileoben.ac.at)
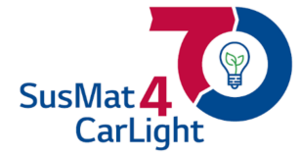
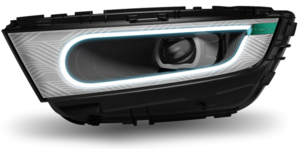
A carlight consists of up to 200 individual parts that have to withstand vibrations and other impacts during driving, high and low temperatures evolving from the environment and during operation as well as chemicals in cleaning agents. This is why the choice of material is particularly important here. In addition, legally compliant light distribution must be guaranteed at all times, even as the carlight ages. Another key problem in carlight construction is that materials "outgas" under certain conditions, causing fogging on optical or critical visual components. Until now, only virgin materials have been able to meet these requirements. However, in order to comply with the EU Green Deal, car manufacturers are required to use more alternative, sustainable materials and construction methods: bio-based, recycled and recyclable.
The project team around ZKW Lichtsysteme (project management), JOANNEUM RESEARCH Forschungsgesellschaft mbH, MATERIALS - Institute for Surface Technologies and Photonics, Polymer Competence Center Leoben GmbH and our two Institutes of Chemistry of Polymeric Materials and Polymer Processing at Montanuniversität Leoben aims to develop new sustainable materials and processes for headlight construction. The focus here is on conventional composite materials and bio-based polymers that not only ensure long-term durability, but in the best case are already made from recycled materials.
Research at the Department of Polymer Engineering and Science primarily focuses on material selection and characterization as well as evaluating the processability of the selected materials in by injection molding. On a laboratory scale, the Institute of Chemistry of Polymeric Materials examines the selected polymers concerning their outgassing and ageing behavior. The use of a suitable material or the addition of special fillers is intended to prevent outgassing. In a further step, the Institute of Polymer Processing produces compounds from promising recycled polymers or biopolymers together with special fillers, which are then processed into test specimens by injection molding. This is followed by rheological and thermodynamic tests as well as simulations to evaluate functionality and recyclability.
More information is provided by E-Mail: Christine Bandl (christine.bandl(at)unileoben.ac.at)
The recycling of polymer waste to high-value materials is an important technology to conserve raw materials based on fossil resources, to reduce the pollution of our environment by plastic waste, and to contribute to decarbonization. In an ongoing project, techniques to up-cycle polyolefin waste are being investigated. This research is conducted in cooperation with PreZero Polymers Austria GmbH (funding by FFG). Here we aim to increase the molar mass of polypropylene (PP) during recycling in order to obtain recycled PP grades ready for processing by extrusion and blow-molding.
It is well known that the molar mass of PP is strongly reduced in the presence of free radicals generated by peroxides or by ionizing radiation. Beta-scission results in a rapid degradation of the PP main chain which is followed by a reduction in viscosity and an increase in the melt flow ratio (MFR), respectively.
To increase the molar mass of PP, specific additives in combination with reactive processing is a promising strategy. First results have shown that the MFR of PP can be reduced significantly with this approach, while the gel-content can be kept quite low. Ongoing research aims at the optimization of the reaction conditions and the further development of this technique to a continuous process.
Another aspect of this research is the reduction of the molar mass of recycled polyethylene (PE). Here, an opposite strategy has to be followed as PE tends to crosslink in the presence of free radicals and under ionizing radiation, respectively. The experimental approach is based on processing of PE at elevated temperatures in the presence of selected additives and catalysts. More information is provided by Wolfgang Kern.
When considering alternative energy carriers, hydrogen-based technologies have a great potential for the future. Hydrogen can be produced by electrolysis or by pyrolysis of natural methane gas. However, the efficient storage of hydrogen remains a major challenge, although various systems for storing hydrogen such as compressed gas and liquefied gas storage already exist.
Another method is based on chemical storage, in which the produced hydrogen is not stored in its pure form, but as a chemical compound after reaction with another component. Metal hydrides are prominent examples for this technology. The advantage of such systems is that (apart from the chemical storage medium) no special equipment is required for the storage of hydrogen, and no uncontrolled release of hydrogen can occur due to the strong chemical bond.
Also, a large number of organic components react with hydrogen. However, some requirements must be met before organic substances can be used in hydrogen storage systems. The organic components must be stable at room temperature and can be repeatedly hydrogenated and dehydrogenated. Typical examples are derivatives of carbazole and dibenzyltoluene.
In the approach followed at our institute, polymers with functional groups that enable the reversible uptake of H2 are synthesized, and tested as novel solid-state storage systems. These storage systems are required to be secure, so that they are suitable for the automotive sector, and also for decentralized storage and generation of electrical energy due to the simplicity of the equipment. More information is provided by Wolfgang Kern and Gisbert Riess.
Under the Paris Climate Agreement (December 2015), global warming must be slowed down and carbon emissions drastically reduced by 80-95% until 2050. A reasonable approach to address this challenge from a long-term perspective is to immediately start the transition of our current energy system, which is still based on fossil fuels. The methane pyrolysis is seen as a potential new process to produce hydrogen as an energy source, without any CO2 emission. The process is based on a thermal or plasma induced cleavage of methane into two molecules of hydrogen and solid carbon according to CH4 → 2 H2 + C. The pyrolysis of natural gas produces 750 kg of high-quality carbon per ton of CH4. Until now, the utilization of carbon from this process has not been in the focus of research.
In this project, building materials are considered as a potential application field for pyrolysis carbon so far. The project aims at the production of surface-functionalized carbon particles, which are solidified in combination with polymer binders (e.g., epoxies) to form highly filled carbon-polymer composites as sustainable building materials. New, very fast and energy-efficient methods for hardening the binder are being investigated, and bio-based epoxy materials will be the first choice in this project. An innovative approach is the use of radiation (X-ray) to achieve the curing process of carbon/epoxy composites. The possibility to work at room temperature represents one of the most attractive features of radiation cured epoxies for the production of advanced composites. Advantages are, e.g., energy savings, low emission of volatile species and improved mechanical properties because of the reduced thermal stresses. An important aspect is the characterization of the carbon/epoxy composites with regard to their mechanical and thermal properties, the remaining porosity, the adsorption behavior (e.g., of pollutants), and the applicability for building materials in terms of pellets and bricks on a large scale. More information is provided by Wolfgang Kern.
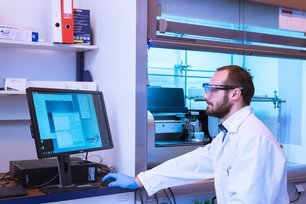
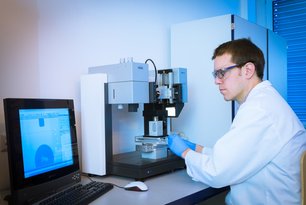
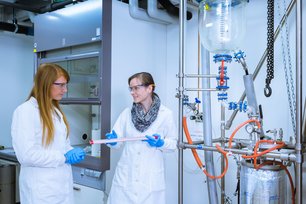
Head of Institute
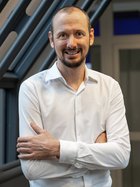
Univ.-Prof. Dipl.-Ing. Dr.techn. Thomas Griesser
thomas.griesser(at)unileoben.ac.at
+43 3842 402 - 2358
Research: Additive Manufacturing, Photopolymerisation, Smart Polymers
Group leaders
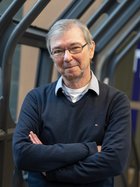
Ao.Univ.-Prof. Dipl.-Chem. Dr.rer.nat. Nicolai Aust
nicolai.aust(at)unileoben.ac.at
+43 3842 402 - 2309
Research: Molecular Characterisation, Analytical Techniques, Safety and Fire Prevention
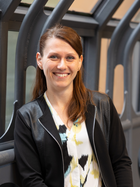
Dipl.-Ing. Dr.mont. Christine Bandl
christine.bandl(at)unileoben.ac.at
+43 3842 402 - 2306
Research: Surface Modification, Surface Characterisation, Polymer Based Coatings
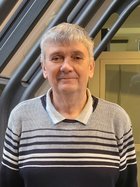
Ass.Prof. Dipl.-Chem. Dr.rer.nat. Gisbert Rieß
gisbert.riess(at)unileoben.ac.at
+43 3842 402 - 2311
Research: Polymer Foams, Flame Retardant Polymers, IT-Management
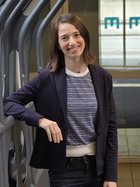
Mag.rer.nat. Dr.rer.nat Alice Lassnig
alice.lassnig(at)unileoben.ac.at
+43 3842 402 - 2350
Research: Printed Electronics
Employees and graduate students
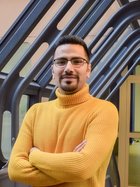
Mag.Dott. Ahmad Alem
sayed.alem(at)unileoben.ac.at
+43 3842 402 - 2373
Research: Surface Chemistry, Energy Storage, Redox Flow Batteries, 2D Materials.
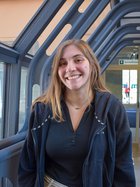
Dott.ssa.Mag. Ilaria Cicco
ilaria.cicco@unileoben.ac.at
+43 3842 402 - 2314
Research: Thiol-epoxy chemistry, bio-based and resource-efficient thermosets, innovative
hardeners and curing strategies and routes for (bio-based) epoxy resins.
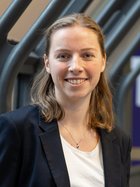
Rita Höller, MSc.
rita.hoeller(at)unileoben.ac.at
+43 3842 402 - 2367
Research: Thiol-Ene Chemistry, DLP-based 3D-printing, Photocurable Vitrimers
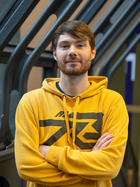
Johannes Krämer, MSc.
johannes.kraemer(at)unileoben.ac.at
+43 3842 402 - 2310
Research: Reactive Extrusion and Upcycling of Polymer Waste Materials, Thiol-Ene Chemistry
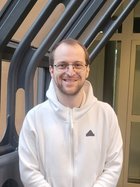
Julian Maier, MSc.
julian.maier(at)unileoben.ac.at
+43 3842 402 - 2323
Research: Surface modification of Thiol-Ene based polymers for the development of
microfluidic systems
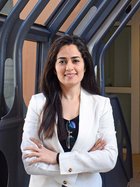
Mag.Dott. Sara Salehi Siouki
sara.salehi-siouki(at)unileoben.ac.at
+43 3842 402 - 2386
Research: Biomolecule-material interface, Photopolymers, Biofunctionalization, Biomaterials
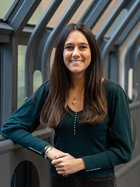
Pauline Vailhe, MA
pauline.vailhe(at)unileoben.ac.at
+43 3842 402 - 2385
Research: Printed Electronics, Strain Sensors, Inkjet Printing
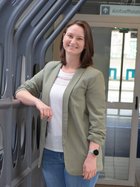
Dipl.-Ing. Nadine Widowitsch
nadine.widowitsch(at)unileoben.ac.at
+43 3842 402 - 2385
Research: Printed Electronics, Inkjet-Printing, Ink Development
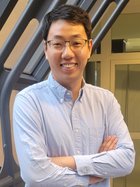
Zizheng, Zhang, MSc.
zizheng.zhang(at)unileoben.ac.at
+43 3842 402 - 2370
Research: Synthesis of surface immobilised photoinitiators
Publications
The Institute of Chemistry of Polymeric Materials plays an active role in the education of students in the field of Polymer Science and Engineering. Teaching comprises the principles of organic polymer chemistry, physical chemistry of polymeric materials as well as selected topics of industrial applications (e.g. coatings technology, fibre materials, elastomers and functional additives) both in lectures and in laboratory courses.
Moreover, elective subjects are devoted to more specialized topics such as polymer photochemistry, polymers in biomedical applications, materials for electronics as well as the technology of adhesives). Numerous external lecturers from industry complement the range of teaching of our chair.
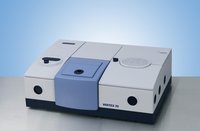
ATR and transmission FT-IR, Spectroscopy, Vertex 70, Bruker Optics
Qualitative and quantitative analysis of the major compounds/chemical structure of solid and liquid samples, reaction kinetics
for further information please contact: nicolai.aust(at)unileoben.ac.at
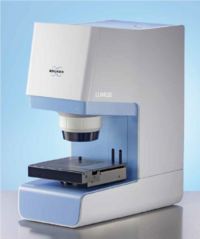
ATR FT-IR microscopy, Lumos, Bruker
Qualitative and quantitative analysis of the major compounds/chemical structure of solid samples in combination with optical microscopy in a defined spot of the sample, mapping mode
for further information please contact: nicolai.aust(at)unileoben.ac.at
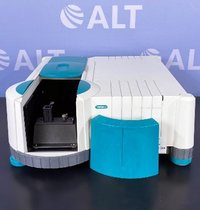
UV-VIS spectroscopy, Cary 50, Varian
Qualitative and quantitative analysis of the absorption characteristics of liquid and dissolved samples
for further information please contact: thomas.griesser(at)unileoben.ac.at
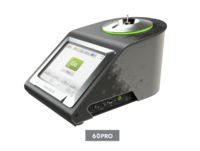
1H and 13C NMR spectroscopy, NMReady-60Pro.nanalysis
Qualitative and quantitative analysis of the chemical structure of liquid or dissolved samples; 60 MHz, Benchtop NMR spectrometer
for further information please contact: gisbert.riess(at)unileoben.ac.at
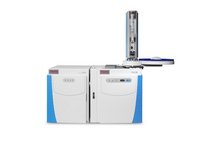
GC-MS, TRACE 1300 (GC) and ISQ 7000 (MS), Thermo Fischer Scientific
Separation as well as qualitative and quantitative analysis of chemical compounds of volatile samples
for further information please contact: gisbert.riess(at)unileoben.ac.at
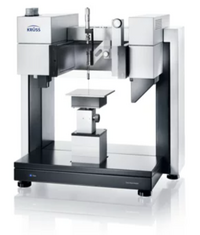
Contact angle goniometer, drop shape analyzer (DSA) 100, Krüss GmbH
Determination of wetting behavior and analysis of surface free energy of solid and plane samples
for further information please contact: christine.bandl(at)unileoben.ac.at
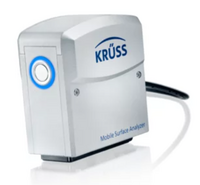
Mobile surface analyzer, mobile surface analyzer (MSA), Krüss GmbH
Determination of wetting behavior and analysis of surface free energy of solid and plane as well as curved samples
for further information please contact: christine.bandl(at)unileoben.ac.at
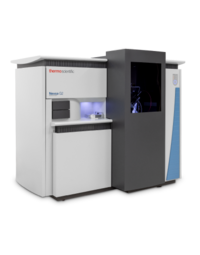
X-ray photoelectron spetrometry (XPS), Nexsa G2, ThermoFisher Scientific
Qualitative and quantitative analysis of elemental surface composition of solid samples, determination of chemical species, mapping and depth profiling of elemental composition
for further information please contact: thomas.griesser(at)unileoben.ac.at
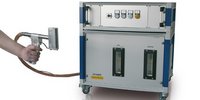
Flame treatment equipment, manual flame treatment, Arcotec GmbH
Oxidative treatment of solid samples, surface pretreatment
for further information please contact: christine.bandl(at)unileoben.ac.at
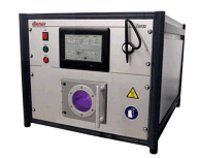
Plasma reactor, Femto, Typ B, Diener electronic GmbH & Co. KG
(Pre)Treatment of solid samples, surface modification and funktionalization; plasma gases aivailable: O2, H2, N2 und NH3
for further information please contact: wolfgang.kern(at)unileoben.ac.at
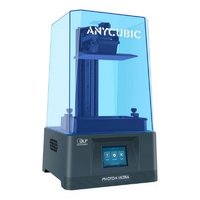
3D printers, Photon Ultra, Photon Mono, Photon Zero, Anycubic
Different LCD based 3D printer for the processing of photosensitive resins.
for further information please contact: thomas.griesser(at)unileoben.ac.at
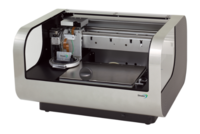
Ink-jet Printer, DMP-2850, Fujifilm
Investigation of the printing behaviour of functional fluids
for further information please contact: thomas.griesser(at)unileoben.ac.at
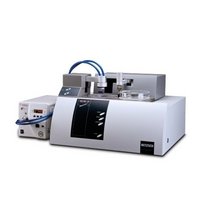
Photo-differential scanning calorimetry, DSC 204 F1 Phoenix, Netzsch
Determination of the reaction kinetics of photoreactive resins.
for further information please contact: thomas.griesser(at)unileoben.ac.at
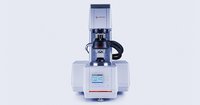
Photo-Rheometer, MCR 102, Anton Paar
Investigation of the network formation of photoreactive resins.
for further information please contact: thomas.griesser(at)unileoben.ac.at
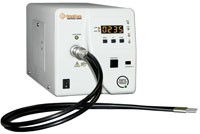
UV equipment lamps (Omicure 1500 and 2000, Excelitas Technologeis Corp.)
spectroradiometer (STS-UV-RAD, Ocean Optics BV)
UV lamps: UV sources with different emission spectra
Spectroradiometer: determination of the emission characteristics of UV sources
for further information please contact: thomas.griesser(at)unileoben.ac.at
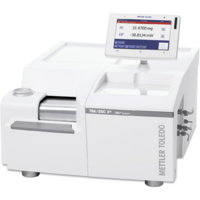
Thermogravimetric analysis, TGA/DSC 3+ STARe System and TGA/DS 1 STARe System, Mettler Toledo
Analysis of thermal stability, evaporation behavior and degree of functionalization of solid samples
for further information please contact: wolfgang.kern(at)unileoben.ac.at
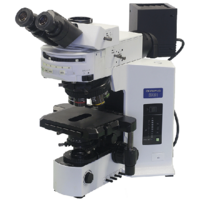
Optical microscope, BX51, Olympus
Optical characterization at 10x – 100x magnification of solid and liquid samples
for further information please contact: wolfgang.kern(at)unileoben.ac.at
Scientific
- East China University of Science and Technology ECUST (CN)
- Erich Schmid Institut (A)
- FH Oberösterreich (A)
- Hydrogen Center Austria (A)
- Joanneum Research (A)
- Johannes Kepler Universität Linz (A)
- Materials Center Leoben GmbH (A)
- Medizinische Universität Graz (A)
- Politecnico di Torino (IT)
- Polymer Competence Center Leoben GmbH (A)
- Technische Universität Graz (A)
- Universität Paderborn (D)
Industry
- 4A Manufacturing GmbH (A)
- Adphos GmbH (D)
- Andritz Hydro (A)
- AT&S (A)
- Atomic Austria GmbH (A)
- Bruno Bock GmbH (D)
- Forestadent GmbH (D)
- Huawei Technologies (D)
- Invision GmbH (A)
- Kufner GmbH (A)
- Luxinergy GmbH (A)
- OK Partner GmbH (A)
- Prezero Polymers Austria GmbH (A)
- Profactor GmbH (A)
- Wollsdorf Leder Schmidt & Co. GmbH (A)
- Würth Elektronik GmbH & Co. KG (A)
- ZKW Lichtsysteme GmbH (A)
Contact & Directions
Institute of Chemistry of Polymeric Materials
Otto Glöckel-Straße 2
8700 Leoben, Austria
+43 3842 402 2301
polychem(at)unileoben.ac.at
Office
4th floor straight ahead of the elevator.