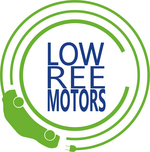
Neodymium (Nd) magnets offer the highest torque densities for electric motors. However, Nd is considered a critical material in Europe because, firstly, demand for this material will exceed production in the coming years and, secondly, mining and processing are not carried out in Europe.
The LowREEMotors project aims to reduce Europe's neodymium dependence by developing magnets in which some of the Nd is partially replaced by less critical materials such as cerium (Ce). However, magnets substituted by Ce have lower magnetic performance than Nd magnets, so electric motors must be redesigned to compensate for the new magnetic properties. The redesign of the motor starts with the alloy composition, followed by the shaping of the magnet by powder injection molding (PIM), and ending with modifications to the motor components.
The LowREEMotors project will develop permanent magnets with 10% less Nd and other rare earth elements (REE). The consortium includes know-how in machine design (Mondragon University and Valeo) and combine extensive expertise in PIM raw material development (Montanuniversität Leoben, Chair of Plastics Processing) and magnet manufacturing (CEA and Magneti Ljubljana). The Katholieke Universiteit te Leuven will perform the LCA to determine the environmental impact of the new magnets and machines.
Partner: Mondragon Goi Eskola Politeknikoa S. Coop. (Mondragon University) –Spain (Lead), Commissariat à l’énergie atomique et aux énergies alternatives (CEA) –France, Katholieke Universiteit te Leuven (KU Leuven) –Belgium, Magneti Ljubljana d.d. – Slovenia, Valeo Powertrain Systems – France
Duration: 2020-2022
Funding: EIT RawMaterials Project Agreement No. 19120
In-mold sensors are very useful for obtaining process information from injection molds. However, they are hardly ever used because they are often too expensive, space in the mold is limited or they are simply not robust enough (cables in the mold). This is exactly where the work at the University of Leoben comes in.
The Chair of Plastics Processing, in close cooperation with the Chair for Automation and the External Institute (both Montanuniversität Leoben), have set themselves the task of making in-mold sensors more robust and cost-effective in order to generate targeted process information and thus, for example, better define the switchover point or more efficiently compensate for rotor systems in multi-cavity molds.