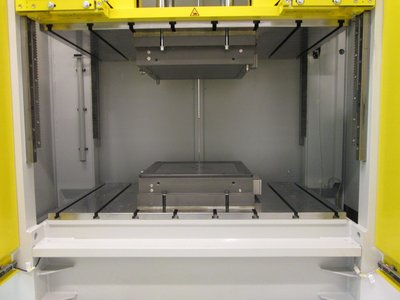
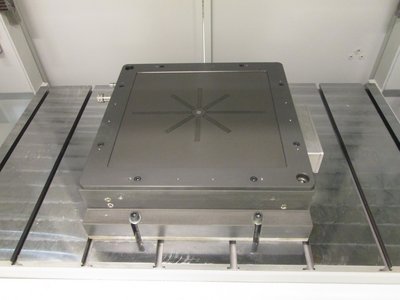
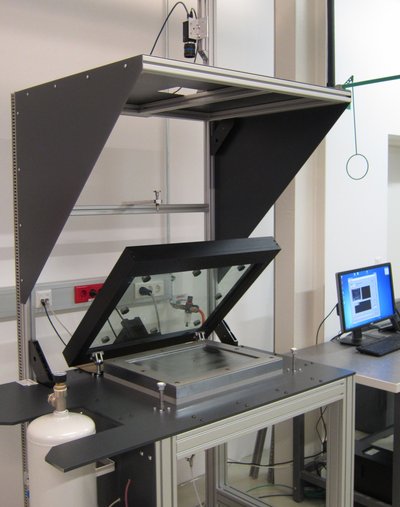
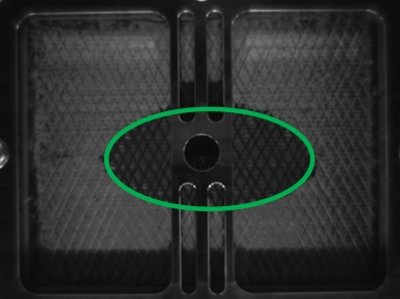
Liquid composite moulding is widely applied for manufacturing lightweight components in the automotive, aerospace, marine, and energy (e.g. wind turbine blades) industries. There, dry preforms made of technical fabrics are impregnated with a viscous resin system. Low cycle time and high component quality, ask for adequate process design based on knowledge of material properties, in particular resin viscosity and fabric permeability. Experimental characterization of fabric in-plane permeability plays a crucial role as it allows for systematic studies and the generation of input for mould filling simulations, which form the basis for process and material optimization. Despite the crucial relevance of permeability data, no standard for its determination has existed up to now.
The path to the ISO Standard
Starting in the 1990s, benchmark studies were initiated to make established methods more robust for industrial use. The topic gained momentum as the scientific community tackled this topic and organized three consecutive international benchmark studies. The Processing of Composites and Design for Recycling Group participated in the last of these, which resulted in guidelines used as a starting point for a standardization project, initiated in 2018. An international team of 30 collaborators conducted studies to clarify remaining questions, and finally came up with a distinct set of specifications for test equipment, design of experiments, specimen preparation, data acquisition and processing (lead by Ewald Fauster), validity checks, and results documentation. As a result, the standard ISO 4410:2023 “Test methods for the experimental characterization of in-plane permeability of fibrous reinforcements for liquid composites moulding” was published in July 2023.
Projectpartner: Centre for Materials and Processes (IMT Nord Europe), Université de Lille, Frankreich, Chair of Carbon Composites, Technical University of Munich, Germany, Department of Mechanical Engineering and Center for Composite Materials, University of Delaware, USA, Department of Mechanical Engineering, Katholieke Universiteit Leuven, Belgium, Department of Polymer Materials and Plastics Engineering, Clausthal University of Technology, Germany, Engineering Development, National Composites Centre, Bristol, United Kingdom, Faculty of Engineering, University of Nottingham, the United Kingdom of Great Britain and Northern Ireland, Faculty of Manufacturing Engineering Technology, Brigham Young University, USA, Faserinstitut Bremen e.V., University of Bremen, Germany, Institut Clément Ader (ICA), Université de Toulouse, CNRS, IMT Mines Albi, INSA, ISAE-SUPAERO, UPS, Albi, France, Institut de Soudure Group, France, Khalifa University of Science and Technology (KUST), Abu Dhabi, United Arab Emirates, Laboratory for Processing of Advanced Composites (LPAC), Institute of Materials (IMX), Ecole Polytechnique Fédérale de Lausanne (EPFL), Lausanne, Switzerland, Leibniz-Institut für Verbundwerkstoffe GmbH, Germany, LMGC, IMT Mines Ales, Univ Montpellier, CNRS, Ales, France, Luxembourg Institute of Science and Technology, Luxembourg, Nantes University, Ecole Centrale Nantes, France, National Physical Laboratory, the United Kingdom of Great Britain and Northern Ireland, Polymers Composites and Hybrids (PCH), IMT Mines Ales, Ales, France, Polyworx B.V., Nijverdal, Netherlands, Processing of Composites Group, Montanuniversität Leoben, Austria, RISE Research Institutes of Sweden, Division Materials and Production, Department Polymers, Fibers & Composites, , Sweden, Robert Bosch GmbH, Hildesheim, Germany
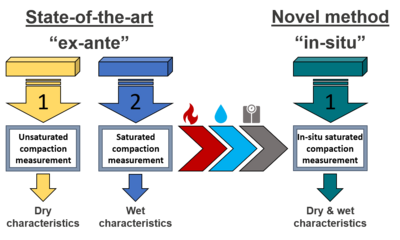
Sustainability as a buzzword of recent years is also gaining more and more importance in complex industrial processes. However, the use of renewable materials or recycling of conventional, i.e. petrochemical, plastics is the most common choice. For high-tech applications, these materials do not always meet the required quality specifications. In these cases in particular, more sustainability can be achieved through process optimisation and the reduction of scrap.
Förderung: bmvit - FTI-Programm: "Nawaro-Flex"
Projektpartner: bto-epoxy GmbH, Kobleder GmbH, Streifeneder ortho. production GmbH, PCCL, MUL - WPK, MUL - KC
Ansprechpartner: Dipl.-Ing. (FH) Marcel BENDER, M.Sc.
Weitere Informationen im Zweijahresbericht 2021 - 2022, (S. 21)
Christian Doppler Laboratory for highly efficient composite processing
Hosted by the Christian Doppler Research Association, supported by grants from the Federal Ministry of Science, Research and Economy (BMWFW) and in cooperation with the FACC Operations GmbH.
Duration: 2013 - 2020
Partner: FACC Operations GmbH
More information can be found here!
Christian Doppler Labor
Cost estimation for efficient composite production
Fiber-reinforced plastics or composite materials have exceptional mechanical properties due to their material combination of high-strength fibers embedded in a resilient polymer matrix. This makes them especially preferable for aerospace and racing applications. But also automotive, transportation, wind energy and sports industry can profit from this materials class’s performance.
But therefor, it is necessary to understand and be able to control the comparatively high material and manufacturing costs of composites. The key to this is cost modelling and estimation for which there are three basic principles available - analogous, parametric and bottom-up. Based on analyzation of these methods and known models a bottom-up/parametric hybrid approach was chosen for the development of the Christian Doppler Laboratory (CDL) cost estimation program ALPHA.
This research is made possible by the Austrian Federal Ministry of Science, Research and Economy, the Christian Doppler Research Association and FACC Operations GmbH.
Partner: FACC Operations GmbH
Further information in the biennial report 2015 - 2016 (page 44)
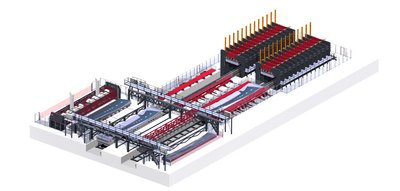
In aircraft manufacturing, fiber-reinforced polymer composites have an enormous potential for fuel savings or increase in range and payload due to their better mass / stiffness ratio compared to metals. Currently, however, the aircraft industry is still heavily influenced by manual activities; this is where Evolution#4 comes in: Based on the Resin Transfer Molding process with integrated quality control as well as concepts of the digital twin, the aerospace sector is to be made fit for Industry 4.0.
Duration: 2018 bis 2020
Funding:FFG, TAKE OFF, 2016
Partner:Alpex Technologies GmbH, Aerospace & Advanced Composites GmbH, BRIMATECH Services GmbH, Fill Gesellschaft m.b.H.
Further information in the biennial report 2017 - 2018 (page 35)
Liquid Composite Moulding
Development and understanding by Research
The processing of composite materials using liquid composite moulding (LCM) has boomed over the last years. This is based on the possibility to automate the process, which is the basis for high volume production. Due to the high interest of the economy on this topic there are a few projects going on at the chair of composite processing. They are dealing with different problems of the LCM process.
Funded by the Ministry for Transport, Innovation and Technology (BMVIT) under the program “Produktion der Zukunft”.
Partner: Alpex Technology GmbH, Austrian Institut of Technology GmbH, Benteler-SGL Composites Technology GmbH, bto-epoxy GmbH, FACC AG
Further information in the biennial report 2015 - 2016 (page 36)
HybridRTM
Quality assured processing technique for material hybrid composites using RTM
In the project “HybridRTM” a one-shot resin transfer molding process is aimed in which the dry fiber based reinforcing structure and a metallic component are placed in the cavity. Infiltration and joining are done in once. Definition of resin injection point and venting gates is necessary. Furthermore, the processing conditions dependent curing and resulting residual stresses are of interest. The aim is to define optimized processing conditions resulting in highest adhesion between composite and metallic component, minimized distortion of the resulting component, and a short cycle time.
Funded by the FFG in frame of research and technology funding under the program “Produktion der Zukunft”, grant agreement no 848666.
Duration: 2015 - 2018
Partner: Benteler SGL Composite Technology GmbH, Austria, alpex technologies GmbH, LKR Leichtmetallkompetenzzentrum Ranshofen GmbH, bto-epoxy GmbH
Further information in the biennial report 2015 - 2016 (S. 32 und S. 41)
Tape placement technologies have been commercially used since 1980's, but the optimization potential has not yet been exhausted. The Processing of Composite Group is working on an in-line process control that will allow in situ consolidation and a stabilization of the process. The group uses a modular, custom-made placement system with a flashlight lamp system.
Duration:2018 - 2021
Funding: FFG, Produktion der Zukunft, 24. AS
Partner: FACC Operation GmbH
Further information in the biennial report 2017 - 2018 (S. 25)
MoVeTech
Model-based processing technique for manufacturing of high quality structural components in aerospace
“MoVeTech” is a project that involves modelling and simulation for composites in aerospace application and it is massively based on sensor assistance. In this project the Advanced Resin Transfer Molding process (also known as gap impregnation process) is analysed. This process is characterized by a gap between the preform and the upper mold. The resin is injected into this gap and afterwards infiltrated into the preform by fully closing the cavity. Different types of sensors (like temperature, pressure, DC or DEA) are used, which provide important processing information like flow front arrival, cure degree and resin crosslinking behavior.
Funded by the FFG in frame of research and technology funding under the program TAKE OFF, grant agreement no 850466.
Durartion:2015 bis 2018
Partner: Langzauner GmbH, FACC Operations GmbH, ALPEX Technologies GmbH, MUL-LA
Further information in the biennial report 2015 - 2016 (S. 24)
NovoTube
"NovoTube", the follow-up project of SCT - Smart Composite Tubes, addresses an alternative approach to decrease filling times and to extend process-related limitations in BARTM. A cascade injection procedure is implemented with the aim of considerably reducing flow lengths during preform saturation.
Funded by Ministry for Transport, Innovation and Technology (BMVIT) and the Austrian Research Promotion Agency (FFG) in frame of the programs “Intelligent Production” and “Production of the Future”.
Duration: 2016 bis 2017
Partner: Partner: Thöni Industriebetriebe GmbH, superTEX composites GmbH, Research Center for Non Destructive Testing GmbH
Further information in the biennial report 2015 - 2016 (page 51)
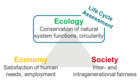
Fiber reinforced polymer (FRP) composites contribute to reaching sustainability goals while simultaneously imposing challenges due to fossil resource use and limited recyclability. The substitution of conventional textile reinforcement and polymeric matrix materials with bio-based alternatives as well as recycling approaches offer promising solutions to overcome these challenges. Nevertheless, the anticipated environmental benefit requires verification. Life Cycle Assessment (LCA) is a useful and suitable method to assess this environmental performance. Methodological choices (on functional unit, system models, impact assessment method, etc.) influence results, therefore, special attention needs to be paid when interpreting results.
Ansprechpartner: Ulrike Kirschnick, MEng, MSc.
Förderung: FFG "Kreislaufwirtschaft 2021"
Projektpartner: MUL - KV,MUL-WPK, Johannes Kepller Universität Linz (JKU), Institute of Technolgy (LIT Factory), Engel Austria GmbH, Leistritz Extrusionstechnik GmbH, Gabriel Chemie
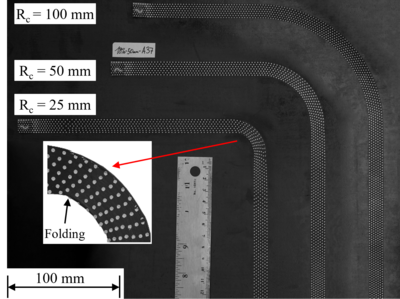
Fibre reinforced plastics have been in increasing demand for years. Automation of composite production processes become crucial to ensure economical production and part reliability. Automated Fibre Placement (AFP) offers the possibility to produce highly optimized parts in terms of weight without compromising mechanical performance.
Ansprechpartner: Dipl.-Ing. Alexander Legenstein
Förderung: Austrian Marshall Plan Foundation, University of Delaware - Center for Composite Materials
Projektpartner: University of Delaware - Center for Composite Materials
Weitere Information im Zweijahresbericht 2021 - 2022, (S. 39)
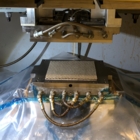

Due to growing concerns in the global sustainability of composite materials, bio-based composites are gaining increasing demand for various semi-structural applications in aerospace, automotive and civil sectors. Bio-based composites are an environmentally friendly alternative to synthetic composites due to their high specific mechanical properties, thermal insulation, good damping properties, good abrasion resistance and low density.
Ansprechpartner: Bharath Ravindran MSc.
Förderung: FFG "Kreislaufwirtschaft 2021"
Projektpartner: MUL - WPK,Kompetenzzentrum Holz GmbH (WoodKplus), Kästle GmbH, bto-epoxy GmbH, R&D Consulting GmbH
Weitere Information im Zweijahresbericht 2021 2022 (S. 65)
RSBC - Reliable and Sustainable composite production for Biobased Components
The project "RSBC" focuses on the development and processing of renewable raw materials based thermoset matrix system for natural fiber reinforced plastics (NFRP)
The goals are the optimization of the material properties, the increase of the biobased carbon content insidethe thermoset system, and the reduction of ecologically and toxicologically harmful contents and excipients. Coordination of both components in the biobased NFRP material and process control contribute to the improvement and adjustments of the material properties for light and structural construction applications. The use of process monitoring methods completes the holistic approach for the prospective successful integration of biobased composites into industrial production processes.
Within the framework of a Life Cylce Analysis, the assessment of material and production processes is carried out under ecological and economic aspects and the analysis of the potential for use of the developed biobased fiber composite materials.
The project is funded by the FFG with funds from the research and technology support within the framework of the FTI Initiative: "Produktion der Zukunft", project number 858688.
Duration: 2017 bis 2020
Partner:Kompetenzzentrum Holz GmbH, Jaksche Kunststofftechnik GmbH, bto-epoxy GmbH, R&D Consulting GmbH & Co KG, Kästle Technology GmbH
![[Translate to Englisch:] SCT Smart Composite Tube [Translate to Englisch:] SCT Smart Composite Tube](/fileadmin/_processed_/b/1/csm_VV_Forschung_SmartCompositeTube_9e9bbbcd66.jpg)
SCT – Smart Composite Tubes
Automated Production of spatially curved fiber composite tubes
A decisive criterion to meet the growing demand for composite materials in industrial applications is the development of highly efficient manufacturing processes. Here, bladder-assisted resin transfer molding (BARTM) represents a suitable process technology for the production of complex shaped hollow parts such as load-bearing frame structures or fluid piping elements.
In frame of the completed research project “Smart Composite Tube”, basic aspects for the realization of a flexible series production of curved composite tubes using braided fiber reinforcements and thermoset resins were studied.
Funded by the FFG in frame of research and technology funding under the program Intelligent Production, grant agreement no 838826.
Durartion: 2013 bis 2016
Partner: Thöni Industriebetriebe GmbH, superTEX composites GmbH, Research Center for Non Destructive Testing GmbH
Further information in the biennial report 2015 - 2016 (page 51)
Stellar
Selective Tape-Laying for Cost-Effective Manufacturing of Optimised Multi-Material Components
The application fields for fiber reinforced composites are more diverse than ever before. Typically the reinforcing materials are based on carbon or glass fibers arranged into technical textiles. In case of high performance components a defined oriented reinforcement is required. Such structures can be reached by using unidirectional reinforced tapes and according placement technologies.
The aim of the “STELLAR” (Selective Tape-Laying for Cost-Effective Manufacturing of Optimised Multi-Material Components) project was to develop a placement technology for thermoplastic based structures. The project was intended to develop a manufacturing process that is appropriate for a wide range of potential applications.
Funded by the European Union Seventh Framework Programme [FP7-2013-NMP-ICT-FOF(RTD)] under grant agreement no 609121.
Duration: 2013 bis 2016
Further information in the biennial report 2015 - 2016 (page 45)