Medizintechnik
In der modernen, patientenorientierten Medizin spielen intelligente Produkte aus polymeren Materialien eine immer bedeutendere Rolle. Dabei treten neben der Anwendbarkeit im klinischen Einsatz auch die Individualisierung von Werkstoffen bzw. die Personalisierung der daraus gefertigten Produkte mehr und mehr in den Vordergrund der Forschung und Entwicklung.
Der Lehrstuhl für Kunststoffverarbeitung beschäftigt sich in diesem Feld mit der Entwicklung und Verarbeitung von polymeren Hochleistungsmaterialien für die medizinische Anwendung in konventionellen sowie additiven Verfahren sowie der Erstellung von medizinischen Modellen aus Kunststoff.
Was wir machen:
- Design von 3D-Druck-Modellen mit taktilem, digitalem Modellierungssystem
- Additive Fertigung von medizinischen Modellen (FFF)
- Werkstoffauswahl für medizinische Einsätze
Kontakt
Ausgewählte Projekte und Forschungsarbeiten
Im Projekt CAMed werden die Möglichkeiten von zwei Materialien für die additive Fertigung für klinische Anwendungen erforscht: der Lehrstuhl für Kunststoffverarbeitung ist dabei für die additive Werkstoffextrusion von polymeren Werkstoffen verantwortlich. Unter anderem sollen metallische Implantate durch Kunststoffe ersetzt werden, die neben dem geringeren Gewicht und ihrer definierten Steifigkeit auch wegen der Durchlässigkeit von Röntgenstrahlen im Vorteil sind.
Durch den Einsatz von maßgeschneiderten Polymeren und unterschiedlichen additiven Fertigungstechnologien für polymere Werkstoffe sollen hochwertige, personalisierte Implantate direkt in den Krankenhäusern gefertigt und dadurch Zeit sowie Kosten gespart werden können. Das Wohl der Patientinnen und Patienten steht dabei sowohl in der Klinik - durch weniger und kürzere Operationen - als auch im täglichen Einsatz der Implantate im Fokus.
CAMed wird von der Österreichische Forschungsförderungsgesellschaft FFG im Rahmen der COMET, K-Projekte, 7. Ausschreibung COMET Projekte 2017 gefördert.
Konsortium: Medizinische Universität Graz Facheinheit für Experimentelle Neurotraumatologie, HAGE Sondermaschinenbau GmbH, Montanuniversität Leoben Lehrstuhl für Kunststoffverarbeitung, Quadrant EPP USA, Inc., Heraeus Deutschland GmbH & Co. KG, ARBURG GmbH + Co KG, JOANNEUM RESEARCH Forschungsgesellschaft mbH, LSS Laser-Sinter-Service GmbH, Technische Universität Graz Institute for Computer Graphics and Vision, Lithoz GmbH, Hofer GmbH & Co KG, FARO Europe GmbH & Co. KG Technische Universität Graz Institut für Maschinenbau und Betriebsinformatik, Montanuniversität Leoben Lehrstuhl für Werkstoffkunde und Prüfung der Kunststoffe, CAE Simulation & Solutions Maschinenbau Ingenieurdienstleistungen GmbH, Ionbond Austria GmbH, voestalpine BÖHLER Edelstahl GmbH & Co KG
Weitere Informationen auch im Zweijahresbericht 2017 - 2018 (S. 30)

Traditionelle Fertigungsmethoden, wie zum Beispiel Spritzgießen, sind für die Fertigung von Einzelstücken wirtschaftlich nicht rentabel. Daher wurde der Einsatz der additiven Fertigung angedacht: Produkte, wie beispielsweise keramische Wärmeelemente für die Hals- und Schulterpartie, können damit ideal an den jeweiligen Träger angepasst werden. Für die Außenseite wird hierbei eine elektrisch isolierende Keramik verwendet und für den inneren Kern ein leitendes Metall.
CerAMfacturing wird im Rahmen des “Horizon 2020” Forschungs- und Innovationsprogramms der Europäischen Union gefördert.
Partner: Fraunhofer-Institut für keramische Technologien und Systeme, Admatec, Ceramicx Ireland Ltd, et al.
Homepage CerAMfacturing
Weitere Informationen auch im Zweijahresbericht 2015 - 2016 (S. 42)
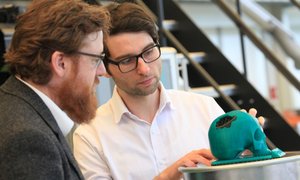
Gedruckte Schädelimplantate aus Kunststoff, direkt im OP noch während der Operation hergestellt. Dieses Ziel verfolgt das FFG Bridge Projekt „iPrint“.
Patientenspezifische, kostengünstige Lösungen gewinnen immer mehr Bedeutung in der Medizintechnik. Additive Fertigungsverfahren („3D-Druck“) können durch ihre Flexibilität und materialeffiziente Arbeitsweise einen Beitrag leisten. iPrint wird dabei ein 3D-Drucksystem für den klinischen Bereich herstellen, das schnell (intraoperativ) und auf den Patienten hinsichtlich Material und Design zugeschnittene Implantate für den Schädelbereich herstellen kann, was schnellere Heilung, bessere ästhetische Resultate und weniger Schmerzen für Patienten und geringere Kosten für das Gesundheitssystem bedeutet.
Das Projekt besitzt eine starke interdisziplinäre Ausrichtung, der maschinenbauliche Aspekt wird von der Obdacher Firma Hage Sondermaschinenbau betreut, die medizinische Seite durch die Meduni Graz und die werkstoffliche Seite durch das Department Kunststofftechnik. Mit diesem Projekt soll das Arbeitsgebiet „Additive Fertigungsverfahren in der Medizintechnik“ mit dem Fokus Materialentwicklung am Lehrstuhl für Kunststoffverarbeitung ausgebaut werden.