Projekte
Im Rahmen von öffentlich geförderten Forschungsvorhaben werden am Lehrstuhl gleichermaßen grundlagenorientierte wie auch anwendungsnahe Fragestellungen bearbeitet.
Hier eine Auswahl von derzeit am Lehrstuhl bearbeiteten bzw. bereits abgeschlossenen Forschungsvorhaben:
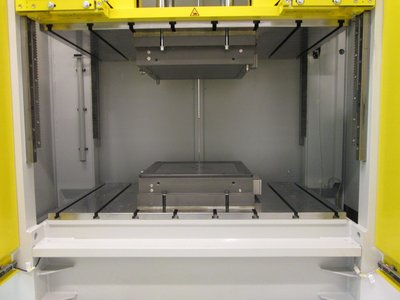
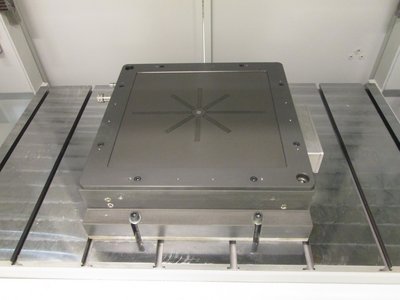
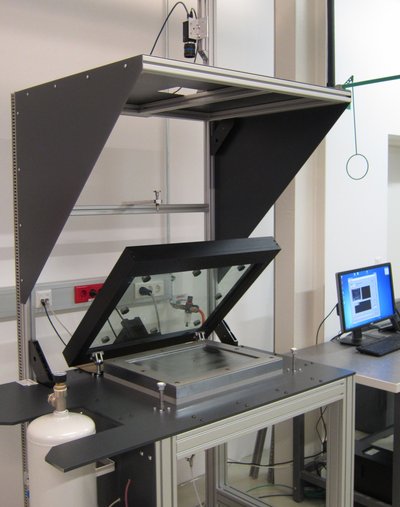
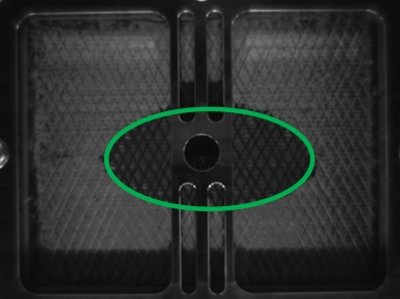
Flüssigimprägnierverfahren werden zur Fertigung von Komponenten im Automobilsektor, der Luft- und Schifffahrt und dem Energiesektor eingesetzt. Dabei werden Preforms, aufgebaut aus Zuschnitten technischer Textilien, mit viskosen Harzsystemen getränkt. Niedrige Zykluszeiten und hohe Bauteilqualität benötigen Prozessdesign auf Basis von grundlegendem Materialverständnis, insbesondere zu Harzviskosität und Permeabilität der Verstärkungsstruktur. Experimentelle Methoden zur Bestimmung der ebenen Permeabilität spielen dabei eine zentrale Rolle. Sie ermöglichen die Bereitstellung von Eingangsdaten für Formfüllsimulationen, die wiederum als Basis für Prozess- und Materialoptimierung dienen. Trotz der Relevanz der ebenen Permeabilität existierte bislang keine Norm für deren Bestimmung.
Der Weg zur ISO-Norm
Ab der 1990er Jahre wurden Studien initiiert, um bestehende Ansätze für industrielle Anwendungen zu ertüchtigen. Diese Bestrebungen nahmen Fahrt auf, als sich die wissenschaftliche Gemeinschaft des Themas annahm und drei aufeinander aufbauende, internationale Vergleichsstudien organisierte. Der Lehrstuhl für Verarbeitung von Verbundwerkstoffen und Design für Recycling hat in der letzten dieser Studien mitgewirkt, die als Startpunkt für ein Normierungsprojekt diente, das 2018 ins Leben gerufen wurde. Ein internationales Team mit rund 30 Partnern erarbeitete diese Studien, um offene Fragen zu klären und Spezifikationen für Prüfstandstechnik, Versuchsplanung, Prüfkörpervorbereitung, Datenaufnahme und -auswertung (geleitet von Ewald Fauster), Plausibilitätsprüfungen und Ergebnisdokumentation zu definieren. Als Ergebnis entstand die ISO-Norm 4410:2023 “Test methods for the experimental characterization of in-plane permeability of fibrous reinforcements for liquid composites molding”, die im Juli 2023 veröffentlicht wurde.
ISO 4410:2023 „Test methods for the experimental characterization of in-plane permeability of fibrous reinforcements for liquid composite moulding“. www.iso.org/standard/79944.html
Projektpartner: Centre for Materials and Processes (IMT Nord Europe), Université de Lille, Frankreich, Chair of Carbon Composites, Technical University of Munich, Germany, Department of Mechanical Engineering and Center for Composite Materials, University of Delaware, USA, Department of Mechanical Engineering, Katholieke Universiteit Leuven, Belgium, Department of Polymer Materials and Plastics Engineering, Clausthal University of Technology, Germany, Engineering Development, National Composites Centre, Bristol, United Kingdom, Faculty of Engineering, University of Nottingham, the United Kingdom of Great Britain and Northern Ireland, Faculty of Manufacturing Engineering Technology, Brigham Young University, USA, Faserinstitut Bremen e.V., University of Bremen, Germany, Institut Clément Ader (ICA), Université de Toulouse, CNRS, IMT Mines Albi, INSA, ISAE-SUPAERO, UPS, Albi, France, Institut de Soudure Group, France, Khalifa University of Science and Technology (KUST), Abu Dhabi, United Arab Emirates, Laboratory for Processing of Advanced Composites (LPAC), Institute of Materials (IMX), Ecole Polytechnique Fédérale de Lausanne (EPFL), Lausanne, Switzerland, Leibniz-Institut für Verbundwerkstoffe GmbH, Germany, LMGC, IMT Mines Ales, Univ Montpellier, CNRS, Ales, France, Luxembourg Institute of Science and Technology, Luxembourg, Nantes University, Ecole Centrale Nantes, France, National Physical Laboratory, the United Kingdom of Great Britain and Northern Ireland, Polymers Composites and Hybrids (PCH), IMT Mines Ales, Ales, France, Polyworx B.V., Nijverdal, Netherlands, Processing of Composites Group, Montanuniversität Leoben, Austria, RISE Research Institutes of Sweden, Division Materials and Production, Department Polymers, Fibers & Composites, , Sweden, Robert Bosch GmbH, Hildesheim, Germany

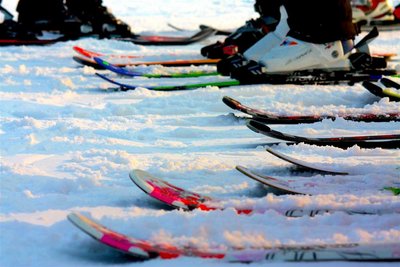
Wintersportartikel wie Ski und Bindung, Ski-Schuhe, Stöcke oder Helme landen am Ende ihres Lebens leider im Sperrmüll und gehen so als wertvolle Rohstoffe für die Herstellung von neuen Produkten verloren. Im neuen interdisziplinären Projekt WINTRUST soll nun der Grundstein für das Recycling von Wintersportartikel und die Kreislaufschließung gelegt werden.
Nach der Sammlung und Zerlegung der Wintersportartikeln bei Projektpartnern werden an der Montanuniversität Leoben Aufbereitungs- und Recyclingversuche an den getrennten Materialien durchgeführt. Eine besondere Hürde im Projekt ist das Recycling der Skier. Hierzu gibt es nur wenige bis keine Erfahrungswerte. Daher zielt die Arbeit in Leoben neben der Entwicklung eines prozessnahen Workflows auch darauf ab, reproduzierbare Realdaten zu erheben und diese dann in Handlungsempfehlungen umzuwandeln. Am Lehrstuhl für Verarbeitung von Verbundwerkstoffen soll dafür eine umfangreiche Lebenszyklusanalyse (life cycle assessment LCA) der oben genannten Prozesse durchgeführt werden: Von der Sammlung bis hin zum neuen Produkt aus dem gewonnen Recyclingmaterial werden die potenziellen Umweltwirkungen und die Energiebilanz systematisch analysiert. Die Berechnungen sollen dabei von Beginn an mitlaufen, nicht wie bei anderen Projekten erst am Ende der Laufzeit erstellt werden. Dies ermöglicht eine frühzeitige Einschätzung der ökologischen und ökonomischen Machbarkeit und damit eine bessere Planbarkeit, sowie Justierbarkeit der Recyclingversuche.
Projektname: WINTRUST (Wintersport Resource Efficiency and improved Circular Economy)
Förderangaben: FFG Collective Research
Projektpartner: ecoplus. Niederösterreichs Wirtschaftsagentur GmbH (Projektleitung), Atomic, Head, Fischer, Blizzard – Tecnica, Leki, Komperdell, Isosport, Hexcel, Gabriel Chemie, Asma GmbH, SUNPOR Kunststoff GmbH, INTERSPORT Österreich, Bründl Sports, GW St. Pölten, Thermoplastkreislauf GmbH, SynCycle, Next Generation Elements GmbH, ZEMKA Gesellschaft m. b. H., Montanuniversität Leoben (Lehrstühle für Kunststoffverarbeitung, Chemie der Kunststoffe sowie Verarbeitung von Verbundwerkstoffen und Design für Recycling), Transfercenter für Kunststofftechnik GmbH, Fachverband der Holzindustrie, VSSÖ – Verband der Sportartikelerzeuger und Sportartikelhänder, Österreichischer Carbon Cycle Circle ÖCC²RDG Recycling Group
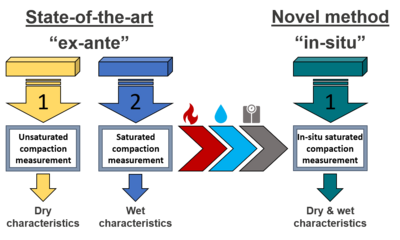
Nachhaltigkeit gewinnt in komplexen Indstrieprozessen stetig an Bedeutung, eine Möglichkeit ist dabei der Einsatz erneuerbarer oder rezyklierter Kunststoffe. Für hochtechnologische Anwendungen erfüllen diese jedoch selten nötige Qualitätsvorgaben. Insbesondere dort wird Nachhaltigkeit durch Prozessoptimierung und Ausschlussvermeidung erreicht.
Förderung: bmvit - FTI-Programm: "Nawaro-Flex"
Projektpartner: bto-epoxy GmbH, Kobleder GmbH, Streifeneder ortho. production GmbH, PCCL, MUL - WPK, MUL - KC
Ansprechpartner: Dipl.-Ing. (FH) Marcel BENDER, M.Sc.
Weitere Informationen im Zweijahresbericht 2021 - 2022, (S. 21)
Betreut durch die Christian Doppler Forschungsgesellschaft und unterstützt durch Fördermittel des Bundesministerium für Wissenschaft, Forschung und Wirtschaft (BMWFW) sowie in Kooperation mit der FACC Operations GmbH.
Laufzeit: 2013 bis 2020
Partner: FACC Operations GmbH
Weitere Informationen finden Sie hier!
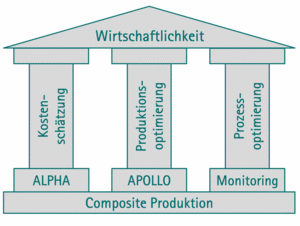
Kostenschätzung für wirtschaftliche Composite Produktion
Faserverstärkte Kunststoffe oder Composite Materialien, besitzen aufgrund ihrer Werkstoffkombination aus hochfesten Fasern in einer widerstandsfähigen Kunststoffmatrix außergewöhnliche mechanische Eigenschaften. Diese werden besonders in der Luft- und Raumfahrt sowie im Rennsport geschätzt. Aber auch die Automotive-, Transport-, Wind- und Sportindustrie können vom Leistungspotenzial dieses High-Tech Werkstoffs profitieren.
Dazu ist es jedoch wichtig die vergleichsweise hohen Werkstoff- und Herstellungskosten zu verstehen und kontrollieren zu können. Die Kostenmodellierung bzw. Kostenschätzung ist hierzu ein essentielles Werkzeug, für das grundsätzlich drei elementare Methoden - Ähnlichkeitsbasierte, Parametrische und Bottom-up Schätzungen - zur Verfügung stehen. Basierend auf einer Analyse dieser Verfahren und bekannter Modelle wurde für das Christian Doppler Labor (CDL) ein Bottom-up/Parametrischer Hybridansatz entwickelt.
Ermöglicht wird diese Forschung durch das Österreichische Bundesministerium für Wissenschaft, Forschung und Wirtschaft, die Christian Doppler Forschungsgesellschaft sowie die FACC Operations GmbH.
Partner: FACC Operations GmbH
Weitere Informationen im Zweijahresbericht 2015 - 2016 (S. 44)
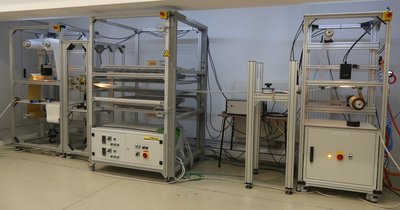
Prepregs are high-quality semi-finished fiber matrix products. During production, textile reinforcement structures are impregnated with a resin matrix. In a subsequent step the prepreg is transferred into its final component geometry.
Ansprechpartner: Mortiz Salzmann MSc.
Förderung: BMK - FTI-Programm "Produktion der Zukunft"
Projektpartner: i-RED GmbH, Isovolta AG
Weitere Information im Zweijahresbericht 2021 - 2022, (S. 51)
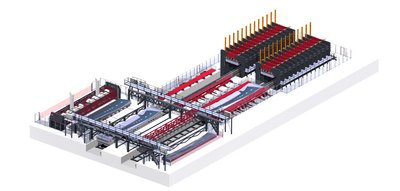
Im Flugzeugbau haben faser-verstärkte polymere Verbundwerkstoffe durch ihr besseres Masse-/Steifigkeits-Verhältnis im Vergleich zu Metallen ein enormes Potenzial zur Treibstoffeinsparung sowie zur Steigerung von Reichweiten und Nutzlast. Aktuell ist die Flugzeugindustrie aber noch stark von manuellen Tätigkeiten geprägt; hier setzt Evolution#4 an: Auf Basis des Resin Transfer Moulding Verfahrens mit integrierter Qualitätskontrolle sowie Konzepten des digitalen Zwillings soll der Aerospace-Bereich fit für die 4. industrielle Revolution gemacht werden.
Laufzeit: 2018 bis 2020
Förderung: FFG, TAKE OFF, Ausschreibung 2016
Projektpartner:Alpex Technologies GmbH, Aerospace & Advanced Composites GmbH, BRIMATECH Services GmbH, Fill Gesellschaft m.b.H.
Weitere Informationen im Zweijahresbericht 2017 - 2018 (S. 35)
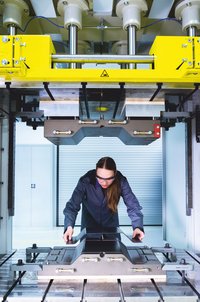
Die Herstellung von Verbundwerkstoffen mittels Flüssigimprägnierverfahren (Liquid Composite Moulding LCM) hat in den letzten Jahren kräftigen Aufschwung erfahren. Grund hierfür ist die Möglichkeit den Prozess zu einem großen Teil zu automatisieren, wodurch die Fertigung von Großserien möglich wird. Aufgrund des großen Interesses der Wirtschaft laufen am Lehrstuhl für Verarbeitung von Verbundwerkstoffen eine Reihe von Projekten, die sich mit unterschiedlichen Fragestellungen des LCM Prozesses auseinandersetzen.
Gefördert durch das Bundesministerium für Verkehr, Innovation und Technologie im Rahmen des Programms “Produktion der Zukunft”.
Partner: Alpex Technology GmbH, Austrian Institut of Technology GmbH, Benteler-SGL Composites Technology GmbH, bto-epoxy GmbH, FACC AG
Weitere Informationen im Zweijahresbericht 2015 - 2016 (S. 36)
Im Projekt „HybridRTM“ wird an einem Einschritt-Harzinjektionsverfahren gearbeitet, bei dem die trockene Verstärkungsstruktur zusammen mit einer metallischen Komponente im Werkzeug platziert wird. Infiltration und Verbindungsaufbau erfolgen dann in einem Schritt. Dafür ist die Definition eines Harzinjektionspunktes und der Entlüftungsöffnungen notwendig. Außerdem sind das prozessbedingte Aushärteverhalten und die resultierenden Eigenspannungen von Interesse. Angestrebt wird die Definition optimierter Prozessbedingungen, mit denen die beste Anhaftung zwischen Verbundwerkstoff- und Metallkomponente, ein minimierter Verzug des Bauteils und möglichst kurze Prozesszeiten erreicht werden.
Gefördert durch die FFG mit Mitteln aus der Forschungs- und Technologieförderung im Rahmen des Programms Produktion der Zukunft, Projektnummer 848666, sowie durch das brasilianische Bildungsministerium und CAPES.
Laufzeit: 2015 bis 2018
Partner: Benteler SGL Composite Technology GmbH, Austria, alpex technologies GmbH, LKR Leichtmetallkompetenzzentrum Ranshofen GmbH, bto-epoxy GmbH
Weitere Informationen im Zweijahresbericht 2015 - 2016 (S. 32 und S. 41)
Tapelegetechnologien werden bereits seit den 1980er Jahren kommerziell genutzt, die Optimierungspotenziale sind dabei aber noch nicht ausgeschöpft. Am Lehrstuhl für Verarbeitung von Verbundwerkstoffen wird an einer in-line Steuerung, die eine in situ Konsolidierung und damit auch eine Stabilisierung des Prozesses ermöglichen soll. Der Lehrstuhl setzt hierfür ein, im Haus entwickeltes, modulares Legesystem, mit einem Blitzlicht-Lampensystem ein.
Laufzeit: 2018 bis 2021
Förderung: FFG, Produktion der Zukunft, 24. AS
Projektpartner: FACC Operation GmbH
Weitere Informationen im Zweijahresbericht 2017 - 2018 (S. 25)
Das Projekt „MoVeTech“ beschäftigt sich mit der Modellierung und Simulation von Verbundwerkstoffen im Luftfahrtbereich und setzt massiv auf Sensorunterstützung. Im Projekt wird der Advanced Resin Transfer Molding Prozess (auch als Spaltimprägnierung bezeichnet) betrachtet. Die geschlossene Kavität weist hierbei zunächst einen Spalt zwischen Oberwerkzeug und Preform auf, in den das Harz eingespritzt und in der Ebene verteilt wird. Der anschließend durch die Presse vertikal ausgeübte Druck verteilt das Harz in der Preform. Dabei werden verschiedene Arten von Sensoren (wie Temperatur, Druck, DC und DEA) verwendet, um wichtige Aspekte des Prozesses wie die Ankunft der Fließfront, den Aushärtungsgrad oder das Vernetzungsverhalten zu erfassen.
Gefördert wird das Projekt durch die FFG mit Mitteln aus der Forschungs- und Technologieförderung im Rahmen des Programms TAKE OFF, Projektnummer 850466.
Laufzeit: 2015 bis 2018
Partner: Langzauner GmbH, FACC Operations GmbH, ALPEX Technologies GmbH, MUL-LA
Weitere Informationen im Zweijahresbericht 2015 - 2016 (S. 24)
„NovoTube“, das Nachfolgeprojekt von SCT – Smart Composite Tubes, beschäftigt sich mit weiterführenden Fragestellungen zum Infiltrationsprozess, bei denen eine Verringerung von Füllzeiten und eine Erweiterung der verfahrensspezifischen Prozessgrenzen im Vordergrund stehen.
Gefördert durch das Bundesministerium für Verkehr, Innovation und Technologie im Rahmen der FTI-Initiativen „Intelligente Produktion” und „Produktion der Zukunft“ und seitens der FFG betreut.
Laufzeit: 2016 bis 2017
Partner: Partner: Thöni Industriebetriebe GmbH, superTEX composites GmbH, Research Center for Non Destructive Testing GmbH
Weitere Informationen im Zweijahresbericht 2015 - 2016 (S. 51)
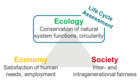
Faserverbundwerkstoffe (FKV) tragen zur Erreichung von Nachhaltigkeitszielen bei, stellen aber gleichzeitig auch Herausforderungen dar aufgrund ihrer Abhängigkeit von fossilen Res-sourcen und begrenzter Kreislaufwirt-schaftsfähigkeit. Die Substitution herkömmlicher textiler Verstärkungs- und Matrixmaterialien durch biobasierte Alternativen sowie Recyclingansätze bieten vielversprechende Lösungen zur Bewältigung dieser Herausforderungen.
Der erwartete Umweltnutzen muss jedoch überprüft werden. Die Lebenszyklusanalyse (LCA) ist eine nützliche und geeignete Methode zur Bewertung dieser Umweltwirkungen. Methodische Entscheidungen (funktionelle Einheit, Systemmodelle, Bewertung der Umweltwirkungen usw.) beeinflussen die Ergebnisse, weshalb bei der Interpretation der Ergebnisse besondere Aufmerksamkeit erforderlich ist.
Ansprechpartner: Ulrike Kirschnick, MEng, MSc.
Förderung: FFG "Kreislaufwirtschaft 2021"
Projektpartner: MUL - KV,MUL-WPK, Johannes Kepller Universität Linz (JKU), Institute of Technolgy (LIT Factory), Engel Austria GmbH, Leistritz Extrusionstechnik GmbH, Gabriel Chemie
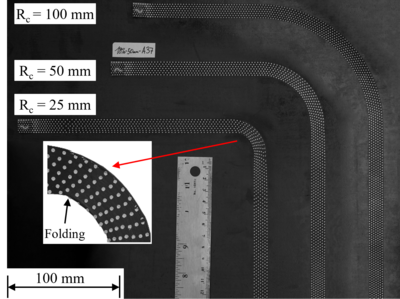
Faserverstärkte Kunststoffe werden seit Jahren immer stärker nachgefragt. Die Automatisierung der Herstellungsprozesse dieser Verbundwerkstoffe ist entscheidend, um eine wirtschaftliche Produktion und Zuverlässigkeit dieser Teile sicherzustellen. Mittels Automated Fibre Placement (AFP) können gewichtsoptimierte Teile hergestellt werden, ohne die mechanische Leistung zu beeinträchtigen.
Ansprechpartner: Dipl.-Ing. Alexander Legenstein
Förderung: Austrian Marshall Plan Foundation, University of Delaware - Center for Composite Materials
Projektpartner: University of Delaware - Center for Composite Materials
Weitere Information im Zweijahresbericht 2021 - 2022, (S. 39)
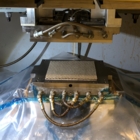

Aufgrund der wachsenden Besorgnis über die globale Nachhaltigkeit von Verbundwerkstoffen, steigt die Nachfrage nach biobasierten Verbundwerkstoffen für verschiedene semistrukturelle Anwendungen in der Luft- und Raumfahrt, und im Automobil- und Zivilsektor. Biobasierte Verbundwerkstoffe sind aufgrund ihrer hohen spezifischen mechanischen Eigenschaften, Wärmeisolierung, guten Dämpfungseigenschaften, guter Abriebfestigkeit und geringer Dichte eine umweltfreundliche Alternative zu synthetischen Verbundwerdkstoffen.
Ansprechpartner: Bharath Ravindran MSc.
Förderung: FFG "Kreislaufwirtschaft 2021"
Projektpartner: MUL - WPK,Kompetenzzentrum Holz GmbH (WoodKplus), Kästle GmbH, bto-epoxy GmbH, R&D Consulting GmbH
Weitere Information im Zweijahresbericht 2021 2022 (S. 65)
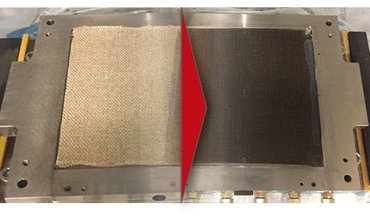
Das Projekt „RSBC“ fokussiert die Entwicklung und Verarbeitung eines auf nachwachsenden Rohstoffen basierenden, duromeren Matrixsystems für naturfaserverstärkte Kunststoffe (NFK).
Ziele sind die Optimierung der Materialeigenschaften, die Erhöhung des biobasierten Kohlenstoffanteils im Duromersystem sowie die Reduktion ökologisch und toxikologisch bedenklicher Inhalts- und Hilfsstoffe. Charakterisierung und Abstimmung beider Komponenten im biobasierten NFK-Verbund tragen zur Verbesserung und gezielten Einstellung der Werkstoffeigenschaften für Leicht- und Strukturbauanwendungen bei. Der Einsatz von Prozessüberwachungsmethoden vervollständigt den ganzheitlichen Ansatz für die zukünftig erfolgreiche Integration biobasierter Verbundwerkstoffe in industrielle Produktionsprozesse.
Im Rahmen einer Ökoeffizienzanalyse finden darüber hinaus die Bewertung von Material und Fertigungsverfahren unter ökologischen und ökonomischen Gesichtspunkten und die Analyse des Einsatzpotentials der entwickelten biobasierten Faserverbundwerkstoffe statt.
Das Projekt wird gefördert durch die FFG mit Mitteln aus der Forschungs- und Technologieförderung im Rahmen der FTI-Initiative: Produktion der Zukunft, Projektnummer 858688.
Laufzeit: 2017 bis 2020
Partner: Kompetenzzentrum Holz GmbH, Jaksche Kunststofftechnik GmbH, bto-epoxy GmbH, R&D Consulting GmbH & Co KG, Kästle Technology GmbH
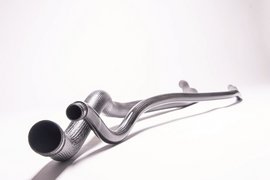
Die Entwicklung von effizienten Verarbeitungsprozessen ist ein entscheidendes Kriterium für den steigenden industriellen Einsatz von Faserverbundwerkstoffen. Das Schlauchblas-RTM-Verfahren stellt hierbei eine geeignete Fertigungstechnologie zur Herstellung komplexer Hohlkörperprofile wie z. B. lasttragende Rahmenstrukturen und integrale Fluidleitungselemente dar.
Im Rahmen des abgeschlossenen Forschungsvorhabens „Smart Composite Tube“ wurden elementare Fragestellungen zur Umsetzung einer flexiblen Serienfertigung von gekrümmten Faserverbundrohren durch Einsatz von geflochtenen Faserhalbzeugen und duromeren Tränkharzen untersucht.
Gefördert durch die FFG mit Mitteln aus der Forschungs- und Technologieförderung im Rahmen des Programms Intelligente Produktion, Projektnummer 838826.
Laufzeit: 2013 bis 2016
Partner: Thöni Industriebetriebe GmbH, superTEX composites GmbH, Research Center for Non Destructive Testing GmbH
Weitere Informationen im Zweijahresbericht 2015 - 2016 (S. 51)
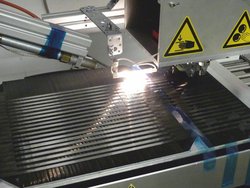
Die Anwendungsgebiete endlosfaserverstärkter Kunststoffverbunde sind heute vielfältiger denn je. Typischerweise werden Verstärkungsmaterialien wie Carbon- oder Glasfasern in Form von technischen Textilien verarbeitet. Für Hochleistungsbauteile werden definiert gerichtete Verstärkungsstrukturen benötigt. Diese lassen sich über unidirektional verstärkte Bändchen mittels Legetechnik herstellen.
Im Projekt „STELLAR“ (Selective Tape-Laying for Cost-Effective Manufacturing of Optimised Multi-Material Components) wurde eine Legetechnik zum Aufbau thermoplastischer Strukturen entwickelt.
Gefördert durch das 7. Rahmenprogramm der Europäischen Union [FP7-2013-NMP-ICT-FOF(RTD)], Projektnummer 609121.
Laufzeit: 2013 bis 2016
Weitere Informationen im Zweijahresbericht 2015 - 2016 (S. 45)